Trattamenti e Finiture
dicembre 2024
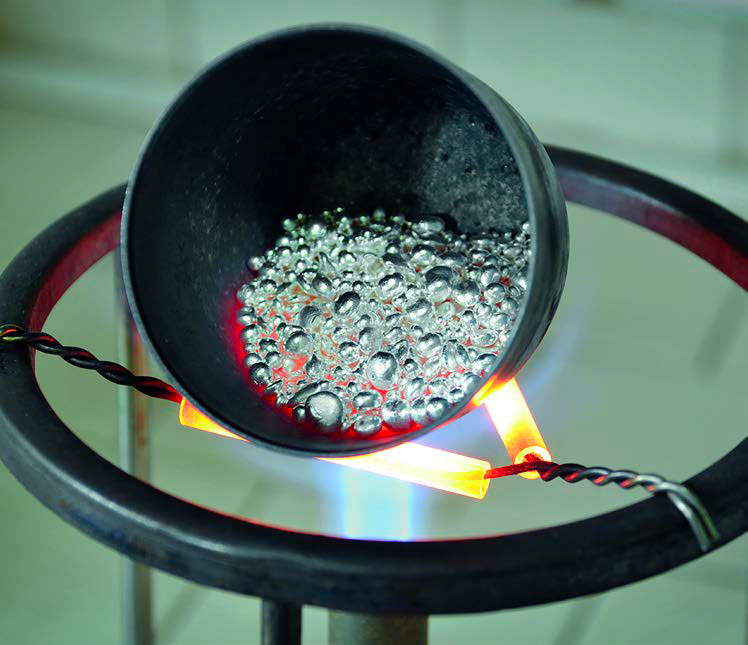
Scarica l’articolo completo in formato PDF
Lavaggio sottovuoto per la produzione di preziosi semilavorati in argento
L’integrazione della lavatrice industriale di IFP nel processo produttivo di La.Met ha rappresentato un importante passo avanti, migliorando la qualità del prodotto, aumentando l’efficienza e riducendo l’impatto ambientale
Metallo prezioso e apprezzato per la sua bellezza e versatilità, l’argento è da secoli un materiale fondamentale in numerosi settori. La sua duttilità e la sua malleabilità lo rendono particolarmente adatto per la creazione di gioielli e altre lavorazioni, mentre l’eccellente conducibilità elettrica e le proprietà antibatteriche lo rendono indispensabile nell’elettronica e in applicazioni innovative, come nella produzione di energia solare, nella farmaceutica e nella cosmetica. Per agevolarne l’uso in qualsiasi applicazione, l’argento deve essere fornito come semilavorato specifico, per soddisfare i requisiti di lavorabilità richiesti. Ed è questa l’attività di cui si occupa La.Met, azienda parte del Gruppo Greggio International, ovvero della produzione e commercializzazione di lastre, nastri, fili, anodi e molte altre tipologie di manufatti per orafi, argentieri, galvaniche e applicazioni industriali, oltre che di recupero e affinazione di ritagli, sfridi e residui di qualsiasi genere di questo metallo.
Leggi di più
Tradizione e innovazione, combinando artigianalità ed evolute tecnologie
«La.Met ha iniziato la propria attività nel 1992 – racconta il direttore di stabilimento, Davide Magnanini – gestendo i primi semilavorati, evolvendosi dalla trafileria, alla laminazione industriale e alla produzione di nastri di argento estremamente sottili, come il nastro centesimale».
Oggi l’azienda svolge la propria attività negli oltre 6.000 mq di superficie produttiva coperta a Caselle di Selvazzano Dentro (PD), dove si è trasferita nel 2002. Vanta una capacità fusoria di oltre 300.000 kg di argento, offrendo prodotti di alta qualità e personalizzazione.
Dotata di una divisione ingegneristica all’avanguardia, di un laboratorio chimico-metallurgico e di un reparto interno di recupero integrale al 100% del materiale, si impegna costantemente nell’innovazione tecnologica e nella sostenibilità ambientale. In questo virtuoso e più ampio progetto di crescita si colloca anche il nuovo impianto di lavaggio mod. KP 1000 MAX, realizzato e installato da IFP Europe.
La struttura organizzativa flessibile e un team altamente specializzato di circa 35 addetti, consentono a La.Met di adattarsi rapidamente alle diverse esigenze dei clienti e alle tendenze dei vari settori serviti. Inoltre, l’appartenenza al Gruppo Greggio International, che include le aziende Rino Greggio Argenterie Spa, Argex Ltd., ha permesso di integrare le proprie competenze, creando sinergie e offrendo un servizio completo che va dalla produzione dei semilavorati alla realizzazione di oggetti artistici in argento. Chiave in questo senso è anche la capacità di mantenere un equilibrio tra tradizione e innovazione, combinando l’artigianalità tipica del settore orafo-argentiero con evolute tecnologie.
Un asset operativo, questo, che ha permesso all’azienda di espandere il mercato, raggiungendo non solo clienti tradizionali ma anche nuovi settori industriali che richiedono semilavorati in argento di alta qualità per applicazioni specifiche.
Qualità e precisione in lastre, nastri, fili e anodi
«La nostra produzione – precisa Magnanini – si articola in quattro macrofamiglie principali: lastre, nastro, materiale di trafilatura e anodi.
Le lastre sono disponibili in una vasta gamma di dimensioni e spessori, con superfici perfettamente planari e strutture molecolari compatte, ideali per lavorazioni complesse».
In particolare, l’azienda rende disponibili lastre con dimensioni fino a 500 x 1.200 mm, in spessori da 0,2 a 14 mm, in leghe con titoli che vanno da 500 a 999‰. Nel reparto taglio possono essere ricavati sottomultipli come quadri, rettangoli, dischi, ovali e sagomati (sia regolari che irregolari) su misura.
I nastri, inclusi quelli centesimali super sottili, sono prodotti con estrema precisione, garantendo risultati eccellenti per vari impieghi come stampaggio, tranciato in continuo e taglio laser. Più nel dettaglio, i nastri sono rifilati e avvolti con cura a vari diametri interni e prodotti con larghezza da 10 a 360 mm, in spessori compresi tra 0,10 e 3 mm; oppure, come nastrini per catene, da 3 a 16 mm di larghezza, in spessori da 0,10 a 0,25 mm. I titoli delle leghe prevedono lo standard con argento 925‰ ma a richiesta anche da 830 fino a 999‰.
«Il nastro centesimale che possiamo realizzare – aggiunge Magnanini – può raggiungere una larghezza di 350 mm, purezza minima Ag 999‰, ed è disponibile in vari spessori fino a 11 micron. Questa è misura di uno dei nostri prodotti di punta e di grande pregio dell’intera gamma».
Disponibili in vari formati sono anche i fili, prodotti in leghe di Ag 835‰, Ag 925‰, Ag 935‰ e Ag 999‰, ideali per essere utilizzati in varie tipologie (tondo, mezzo tondo, quadro ecc.) sia da piccoli artigiani che da grandi industrie, per esempio nella contatteria elettrica.
«Partendo da un semilavorato da 10 mm – precisa lo stesso Magnanini – siamo in grado di arrivare a diametri fino a 0,25 mm, offrendo fili con ottime caratteristiche di lavorabilità e alti standard qualitativi».
Gli anodi, con purezza minima di Ag 999‰, sono invece impiegati in processi galvanici ed elettrodeposizione. L’azienda produce diverse tipologie di anodi, tra cui sezioni a “osso di cane”, anodi corrugati, filo tranciato e granella, rispondendo alle diverse esigenze dei processi industriali.
Sistema integrato per qualità, ambiente e sicurezza
Nel corso degli anni, La.Met ha sempre mantenuto un forte impegno verso l’innovazione e la sostenibilità ambientale.
«Non ci sono stati cambiamenti sostanziali nel processo di sviluppo del prodotto – afferma Magnanini – ma le prerogative a livello di ambiente e sostenibilità hanno subito da qualche anno una decisa accelerazione rispetto al passato. L’obiettivo è stato quello di introdurre in azienda un sistema integrato per qualità, ambiente e sicurezza».
Con particolare riferimento alle fasi di lavaggio, è stato per esempio eliminato l’uso di percloroetilene.
«Abbiamo scelto IFP Europe come partner – sottolinea Magnanini – non solo per la positiva esperienza della nostra consociata Rino Greggio Argenterie, che da quasi un decennio utilizzava un impianto dello stesso costruttore, ma anche perché ci offriva prerogative che le macchine a tunnel come quella in nostro uso, non potevano fornire».
«La sfida vinta – conferma con soddisfazione Magnanini – è stata quella di identificare i parametri corretti affinché la qualità della pulizia dei prodotti lavati fosse costante e ripetibile. Grazie a un lavoro di squadra e alla disponibilità del costruttore nel seguire le nostre specifiche esigenze, è stato possibile mettere a punto un processo ottimale. In questo percorso l’Ing. Filippo Rossi, referente di IFP, si è dimostrato molto disponibile e preparato nel supportarci e affiancarci durante tutte le fasi di implementazione».
Benefici operativi e miglioramento del flusso produttivo
L’introduzione del nuovo impianto IFP Europe in La.Met ha portato numerosi benefici, ridefinendo l’intero flusso di lavoro del reparto lavaggio.
«L’approccio batch del sistema – conferma Magnanini – che rispecchia il concetto di “one piece flow”, ha portato al nostro interno vantaggi significativi in termini di efficienza operativa e qualità del prodotto. In questo senso abbiamo eliminato operazioni a basso valore aggiunto e migliorato in modo rilevante la qualità superficiale dei prodotti, garantendo superfici senza aloni e non opacizzate, anche dopo il ciclo termico di ricottura».
Uno dei principali vantaggi è stato l’integrare la fase di carico con l’operazione di taglio delle lastre, eliminando due fasi separate di carico e scarico presenti nel precedente sistema a tunnel. La configurazione statica della macchina, pur consentendo il basculamento del cestello (per ora non utilizzato da La.Met), evita problemi di sfregamento e contatti dovuti alla traslazione, garantendo superfici impeccabili prive di striature e ammaccature.
«La flessibilità dei programmi di lavaggio della nuova KP 1000 MAX di IFP Europe – continua Magnanini – permette di trattare efficacemente tutte le tipologie di prodotto, sia di laminazione che di trafilatura, senza i vincoli precedentemente imposti dal sistema a tunnel. Questa versatilità si traduce in una maggiore efficienza produttiva e in una qualità del prodotto finale costantemente elevata».
Inoltre, il sistema batch si allinea perfettamente con la modalità di lavoro pull adottata da La.Met, dove la disponibilità delle lastre non supera mai l’effettiva capacità dei cesti di 12 lastre per batch.
«Questo sincronismo tra la capacità produttiva e il flusso di lavoro – rileva Magnanini – ha permesso di ottimizzare i tempi di ciclo, che si attestano intorno ai 15 minuti, sufficienti per gestire efficacemente il volume di produzione».
Impatto ambientale e sicurezza: priorità assolute nel processo innovativo
Uno dei punti di forza della nuova tecnologia di lavaggio IFP Europe è il suo impatto positivo sull’ambiente e sulla sicurezza dei lavoratori, aspetti che La.Met considera prioritari nella sua strategia di crescita.
«Il trattamento sottovuoto – evidenzia Magnanini – assicura una maggiore garanzia ambientale, sia nell’area di lavoro che verso l’esterno.
La depressurizzazione impedisce la fuoriuscita di vapori, mentre i sistemi di sicurezza governano efficacemente ogni fase del processo. L’assenza di contatto diretto tra operatori e liquidi di lavaggio incrementa notevolmente la sicurezza sul lavoro, eliminando potenziali rischi per la salute».
Tutto questo si inserisce in una strategia più ampia dell’azienda volta a ridurre i fattori di rischio per le persone e l’ambiente. Negli ultimi tre anni, l’azienda ha intrapreso numerose iniziative in questa direzione, come la rimozione di cementi con componenti cancerogeni nella fonderia di colata continua, optando per materiali ecologici.
«Abbiamo iniziato a utilizzare materassini e prodotti ecologici – conferma Magnanini – per ridurre i fattori di rischio per le persone. Questi cambiamenti non solo migliorano la sicurezza e la salute dei lavoratori, ma contribuiscono anche a ridurre l’impatto ambientale complessivo».
Crescita continua puntando su eccellenza produttiva e responsabilità ambientale
Come già sottolineato, l’investimento nel nuovo impianto di lavaggio acquisito da IFP Europe si inserisce in una strategia di crescita continua a lungo termine di La.Met, volta a mantenere e rafforzare la sua posizione di rilievo nel settore dei semilavorati in argento.
«Questa tecnologia – conclude Magnanini – non solo migliora la qualità dei nostri prodotti e l’efficienza dei processi, ma ci posiziona all’avanguardia in un mercato sempre più attento alle tematiche ambientali e di sicurezza».
L’azienda guarda dunque al futuro con l’obiettivo di continuare a evolversi e innovarsi, mantenendo un focus costante sull’eccellenza produttiva e la responsabilità ambientale. La certificazione UNI EN ISO 9001:2015, la RJC (Responsible Jewellery Council), il riconoscimento Cribis Prime Company e il prossimo ottenimento della certificazione energetica ISO 14001, testimoniano l’impegno profuso verso un modello di business sostenibile e responsabile su tutti i fronti.
La.Met sta esplorando nuove opportunità di crescita, sfruttando la flessibilità produttiva offerta dalle nuove tecnologie per diversificare la propria offerta e penetrare nuovi segmenti di mercato.
IL CUORE PULSANTE DELLA PRODUZIONE, DALLA PROGETTAZIONE ALLA COLATA
La.Met dispone al proprio interno di un engineering division, equipaggiata con sofisticate attrezzature CAD/CAM 2D/3D, che permette la realizzazione di prodotti su misura, e di un laboratorio chimico-metallurgico. Anch’esso dotato di strumentazioni avanzate come la titolazione potenziometrica volumetrica e la spettroscopia di emissione ottica al plasma accoppiato induttivamente, consente un monitoraggio costante e preciso di tutto il processo produttivo. In particolare, il processo produttivo, una capacità fusoria di oltre 300.000 kg/anno.
L’origine è la materia prima che arriva sotto forma di granella, lingotti, sfridi e roda di rame.
La flessibilità produttiva consente all’azienda di rispondere efficacemente alle diverse esigenze del mercato, mantenendo costanti gli elevati standard qualitativi che la contraddistinguono nel settore.
L’azienda ha investito molto nell’innovazione dei processi, come evidenziato, oltre che dall’integrazione del nuovo impianto di lavaggio mod. KP 1000 MAX di IFP Europe, dall’introduzione di lavorazioni CNC di fresatura a tre assi (fino a 36.000 giri/min e 600 x 1.000 mm lavorabili), tornitura CNC (fino a 300 x 800 mm) e sistemi di elettro-erosione a filo (con precisione centesimale garantita e raggiatura minima 0,2 mm). Questi investimenti tecnologici non solo migliorano la qualità dei prodotti, ma aumentano anche l’efficienza e la flessibilità produttiva di La.Met.
LAVAGGI PERFETTI A BASSO CONSUMO SU GRANDI VOLUMI
Per soddisfare le proprie esigenze di lavaggio industriale, La.Met ha scelto di acquistare un impianto della serie KP.MAX prodotto da IFP Europe.
Questa gamma comprende diversi modelli, tutti contraddistinti da una camera di lavaggio di ampie dimensioni, che consente un trattamento efficace sia per alti volumi produttivi sia per carichi singoli di dimensioni notevoli. Queste lavatrici industriali operano completamente in condizioni di vuoto, garantendo un ciclo di lavoro che risponde perfettamente alle necessità di produzione su larga scala, mantenendo tempi operativi relativamente contenuti. In particolare, il modello KP 1000 MAX, selezionato da La.Met per potenziare il proprio reparto produttivo, presenta caratteristiche tecniche di rilievo, tra cui la capacità di accogliere cesti d’ingresso con dimensioni massime fino a 700 x 1.000 x h600 mm e un carico massimo di 800 kg cadauno. Il funzionamento della macchina avviene sotto vuoto in tutte le fasi del processo, il che garantisce l’ermeticità dell’intero sistema e l’assenza
di residui sui componenti trattati. Questo modello è stato progettato con due obiettivi principali: la riduzione dei consumi energetici e il recupero dell’olio utilizzato, che può essere nuovamente impiegato nel ciclo produttivo, con conseguente risparmio sui costi. Un altro aspetto rilevante di questa macchina è la sua progettazione mirata a minimizzare le operazioni di manutenzione. Le camere di lavaggio sono completamente autopulenti, eliminando il rischio di accumuli di residui sul fondo o di incrostazioni. Di conseguenza, non è necessario intervenire manualmente per aprire serbatoi, camere o distillatori a scopo di pulizia.
La macchina offre anche un sistema avanzato di distillazione del solvente, che, in combinazione con i sistemi di filtrazione e separazione dell’olio, assicura un processo di lavaggio ottimizzato, riducendo sia i costi di smaltimento dei rifiuti sia quelli legati alla gestione complessiva.
CE QU'ILS DISENT DE NOUS
Vous trouverez ci-dessous quelques articles écrits par nos clients et publiés dans les publications du secteur, décrivant leurs activités et comment leur utilisation de nos équipements de lavage sous vide contribue à la qualité de leurs produits.