JUNE 2014
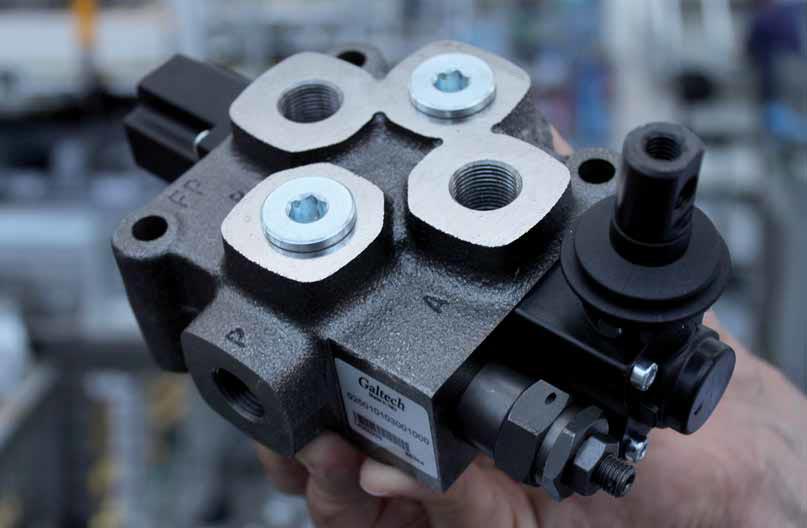
Scarica l’articolo completo in formato PDF
GALTECH
Dal percloroetilene agli alcoli modificati per il lavaggio di componenti oleodinamici: un percorso virtuoso
Il lavaggio a percloroetilene, come si legge anche in alcuni degli articoli precedenti, è ancora in uso per svariate applicazioni, laddove mostra di poter ottenere risultati di lavaggio che altri sistemi non riescono a raggiungere, vuoi per il tipo di contaminazione presente sui pezzi, vuoi per la loro particolare conformazione e per il materiale di costruzione, vuoi per i requisiti di pulizia che variano molto da applicazione ad applicazione. Tuttavia, sempre più numerose sono le aziende che sfruttano le nuove tecnologie di lavaggio a solvente a basso impatto ambientale per sostituire il percloroetilene come agente di lavaggio, a beneficio non solo di ambiente e salute ma anche di uno snellimento del flusso produttivo e di una maggiore rapidità di lavorazione. Quella che segue è l’esperienza di Galtech, azienda storica operante nel settore dell’oleodinamica, che nell’ambito di un rifacimento complessivo del layout dello stabilimento produttivo, nel 2013 ha scelto di investire in una macchina di lavaggio sottovuoto ad alcoli modificati di IFP Europe di Cittadella (PD) in sostituzione delle vecchie macchine a percloroetilene, ormai inadeguate a soddisfare i requisiti di qualità e di produttività dell’azienda.
Leggi di più
Chi è Galtech
Galtech da oltre 50 anni si propone come azienda di riferimento nella produzione di apparecchiature oleodinamiche. Fondata nel 1955 a Reggio Emilia come Iotti & Strozzi, l’azienda inizia ad operare in un settore allora emergente: il controllo dell’energia dei fluidi. Pompe ad ingranaggi, motori, valvole e cilindri sostituiscono velocemente vecchie ed ingombranti trasmissioni meccaniche. L’allora scarsa conoscenza della nuova tecnologia e la perplessità degli utilizzatori vengono gradualmente superate dalla grande disponibilità dell’azienda: i prodotti sono costantemente perfezionati, le applicazioni si moltiplicano, il mercato si espande. La società, passata ad una produzione in serie, si dota di una struttura e di una mentalità industriale moderna e dinamica. Nel 1992 entra a far parte del Gruppo industriale e finanziario Gallinari, mutando il nome in Galtech, e nel 2011 entra nel suo capitale sociale un importante partner strategico, il Gruppo Interpump, società internazionale che opera nel settore dell’acqua in pressione e dell’oleodinamica. “Galtech fattura 15 milioni euro/anno e produce pompe a ingranaggi esterni, valvole idrauliche e distributori oleodinamici principalmente destinati al mercato della rivendita – esordisce Achille Grossi, consulente di produzione per Galtech – Lo scorso anno si è fusa con Hydrocontrol di Osteria Grande (BO), anch’essa dedicata alla produzione di distributori oleodinamici primo impianto per gli OEM. Nell’ambito di questa fusione, la proprietà ha deciso di investire nel rifacimento della sede e del layout dello stabilimento Galtech a Reggio Emilia, cercando di risolvere alcune criticità produttive che pregiudicavano il raggiungimento di determinati obiettivi, fra cui quello di minimizzare l’impatto ambientale della produzione, migliorare le condizioni di lavoro in alcune fasi produttive e snellire l’intero processo. Abbiamo impostato il nuovo stabilimento sui criteri della lean production ed è rientrato in questi interventi migliorativi anche il processo di lavaggio finale dei nostri pezzi, una fase che riguarda il 100% della nostra produzione. Grazie alla partnership con IFP Europe, che ci ha trasferito tutta la sua esperienza nel lavaggio sottovuoto ad alcol modificato, abbiamo eliminato un prodotto borderline come il percloroetilene, abbiamo velocizzato e snellito la produzione, e abbiamo sollevato i nostri operatori da alcuni compiti che prima erano necessari per ottenere la qualità di lavaggio che la sola macchina a percloro non garantiva”.
Un flusso produttivo molto corto
“Galtech produce distributori oleodinamici, cioè valvole di distribuzione dei fluidi verso cui converge la portata della pompa idraulica azionata da un motore diesel o elettrico, il cuore dell’impianto oleodinamico di macchine agricole e movimento terra, piattaforme di sollevamento, carrelli elevatori ” – spiega Grossi. Il ciclo di produzione oggi è veloce e uniforme. Le fusioni in ghisa grezze sono lavorate meccanicamente con un processo in due fasi su centri di lavoro a controllo numerico che asportano il truciolo. Successivamente i pezzi subiscono un lavaggio estremamente accurato che ha il compito di rimuovere il truciolo residuo e le emulsioni (acqua e olio) di lavorazione. Si tratta di un lavaggio di finitura, perché una volta uscito dall’impianto di lavaggio, il pezzo subisce solo una fase ulteriore di superfinitura (lappatura) dei fori che alloggiano i cursori di distribuzione. L’olio intero usato durante la lappatura viene lasciato all’interno del pezzo come protettivo. Dopodiché i pezzi sono montati e testati prima della spedizione.
Dal percloro all’alcol modificato: un percorso virtuoso
“Tutta la nostra produzione viene lavata. Basta questo per dire quanto importante sia per noi avere una impianto di lavaggio all’avanguardia ed efficiente, in grado di fornire qualità senza impattare su ambiente e operatori, bensì inserendosi nella logica di lean production su cui abbiamo impostato tutto il nuovo stabilimento – afferma Achille Grossi. “Con IFP abbiamo fatto un percorso virtuoso di passaggio dal percloroetilene all’alcol modificato come agente di lavaggio, un percorso che ha portato alla drastica riduzione del consumo di solventi e dello smaltimento di fanghi, un percorso che ha imposto una nuova strada da percorrere anche per le altre aziende del gruppo, perché ha portato ottimi risultati, sia nella pulizia del pezzo che nel processo globale, dall’abbattimento del tempi di attraversamento al funzionamento delle macchine senza presidio”. “Siamo stati i primi ad acquistare una macchina IFP, poi abbiamo trascinato in questa scelta anche Hydrocontrol che ha pianificato l’acquisto di altre tre macchine, due per loro e una ulteriore per noi, la cui consegna è prevista per l’agosto del 2014 – interviene Davide Cottafava, responsabile macchine utensili e CNC – Abbiamo 5 linee di lavorazione con cui produciamo circa 600 pezzi/giorno. Attualmente abbiamo 3 macchine di lavaggio ma con l’arrivo della seconda macchina IFP andremo a sostituirne 2, quindi in futuro laveremo con due impianti l’output di 5 linee”. “L’integrazione di un nuovo processo di lavaggio era una operazione da ponderare attentamente, perché abbiamo necessità di lavorare la ghisa e lavarla immediatamente, senza che passi del tempo tra un’operazione e l’altra – prosegue Grossi – non potevamo quindi permetterci sbagli. Devo dire che la macchina di lavaggio IFP, rispetto a quelle che ho visto passare negli anni, è molto performante e ha minori costi di gestione e manutenzione”.
I vantaggi del nuovo sistema
Quella installata da IFP Europe è una macchina sottovuoto ad alcool modificato in linea con le altre macchine di lavorazione meccanica. Il lavaggio avviene ad immersione con cestello in rotazione di 360°C, senza emissioni in atmosfera, con un consumo ridotto di energia e minimo di solvente. Con la precedente tecnologia a percloroetilene, i pezzi dovevano essere soffiati manualmente dall’operatore per rimuovere il truciolo dalle canalizzazioni dei distributori. Il soffi aggio comportava un rallentamento del flusso produttivo e risultati molto variabili poiché l’efficacia dipendeva strettamente dalla manualità di ogni operatore. Senza contare che si trattava di un’operazione molto impattante e gravosa. Tuttavia, rappresentava l’unico modo per raggiungere il livello di qualità desiderato, perché era in questa fase che si rimuoveva la maggiore quantità di truciolo, più che nella fase di lavaggio. La macchina a percloro, inoltre, comportava una manutenzione e una gestione delle morchie gravosa, sia dal punto di vista dei costi che dell’impatto ambientale e sugli operatori incaricati. “Con l’installazione delle macchine IFP abbiamo abolito l’operazione di soffiaggio – dichiara Davide Cottafava – il truciolo in ghisa esce dal lavaggio asciutto e la manutenzione del distillatore è semplice, sicura e veloce. La produttività è molto elevata: con questa macchina laviamo circa 250 pezzi/ giorno e quando sarà installata anche la seconda, che ne sostituirà due diverse, laveremo circa 400 pezzi in più al giorno, di varie forme e dimensioni, coprendo l’intero fabbisogno di Galtech. I consumi di prodotto di lavaggio, che con il percloro erano alti e al limite del consentito, oggi sono quasi ridotti a zero: utilizziamo un alcol modificato di DOW e stiamo ancora impiegando il prodotto della prima fornitura acquistata”.
Cosa dicono di noi sulle testate di settore
Di seguito alcuni articoli, realizzati da nostri clienti, in cui vengono descritte le caratteristiche delle loro attività e come l’utilizzo dei nostri impianti di lavaggio sottovuoto contribuiscono alla realizzazione qualitativa dei loro prodotti.