Trattamenti e Finiture
Dicembre 2021
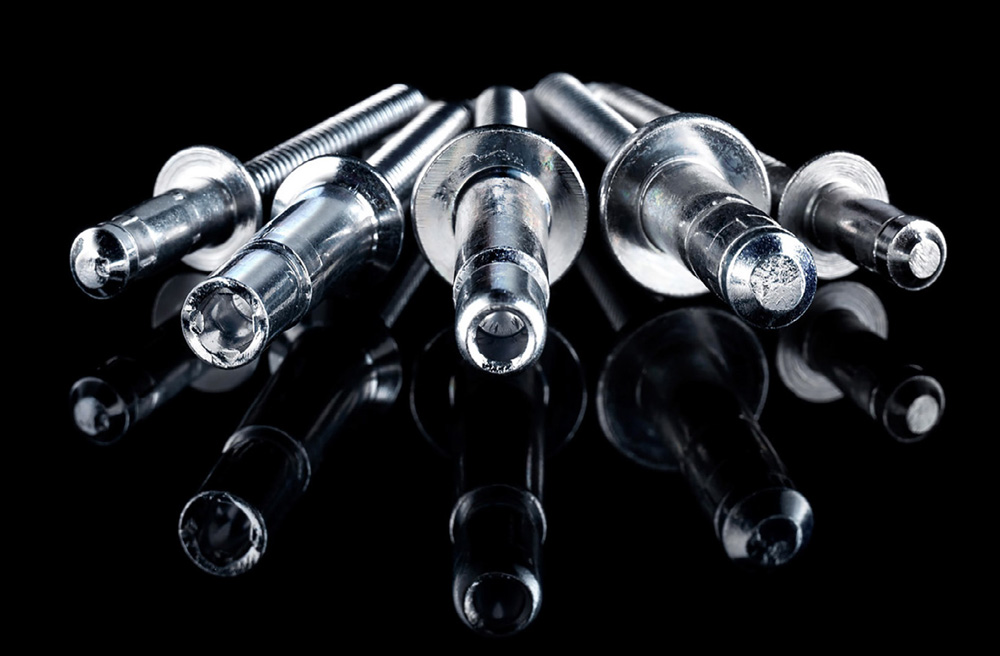
Scarica l’articolo completo in formato PDF
LAVAGGIO “AL TOP” DEI COMPONENTI
Sariv è in grado di studiare e realizzare le soluzioni più avanzate per risolvere ogni problema di fissaggio. Svariate tipologie di rivetti a strappo e inserti filettati, la cui qualità garantita anche dalla loro perfetta pulizia e decontaminazione. Queste ultime sono ottenute con un lavaggio sottovuoto ad alcoli modificati effettuato su un performante ed ecosostenibile impianto IFP Europe
Nata poco più di una trentina d’anni fa come sviluppo aziendale di un gruppo di proprietà familiare, già operante in altre industrie nel settore meccanico, Sariv ha fatto del rivetto a strappo e dell’inserto filettato una vera e propria specializzazione. Stiamo infatti parlando di componenti altamente personalizzate in grado di risolvere qualunque problema di fissaggio, che oggi si traducono in oltre 3 milioni di pezzi al giorno, realizzati nei 9.000 mq coperti dei due plant produttivi di Fontaniva (PD). Una produzione che trova applicazione in svariati settori, con una quota export che raggiunge l’85%.
«Oltre all’automotive – precisa l’amministratore delegato, ing. Nicola Sartore – alla quale ogni giorno è destinata più della metà della nostra produzione con soluzioni custom su singola specifica, annoveriamo tra i settori più serviti quello delle strutture metalliche, l’elettrodomestico, oltre a segmenti più di nicchia che necessitano comunque di soluzioni di fissaggio pensati e realizzati ad hoc».
Leggi di più
Peculiarità distintiva dell’azienda è infatti quella di applicare ogni giorno know-how ed esperienza per risolvere problemi di fissaggio e per creare soluzioni innovative per i prodotti dei propri clienti. Chiave in questo senso è stato il 2012, anno in cui, grazie agli investimenti fatti in ambito tecnologico e tecnico, è avvenuto un decisivo passaggio da azienda di produzione “seriale” legato più alla produzione standard, a realtà specializzata nel problem solving per soluzioni di fissaggio. Evoluzione del modello di business coincisa anche con il passaggio al digitale e alla digitalizzazione dei processi che ha permesso di fare passi da gigante in termini di possibilità di controllo e di sviluppo dei progetti. «La digitalizzazione – ribadisce l’ing. Sartore – ha dato la possibilità di poter avere accesso ad applicazioni per noi impossibili da raggiungere senza la trasformazione avvenuta. Il nostro mercato principale è divenuto l’automotive, dove il risk management è spinto, e la possibilità di ottenere dati in tempo reale per controlli real-time degli andamenti dei processi, e di gestione degli scostamenti ha fatto la differenza. Per una azienda di modeste dimensioni come la nostra e con un prodotto povero, non sarebbe stato pensabile avere il “controllo” sui prodotti montati su una moltitudine di automobili se non avessimo intrapreso un percorso simile».
Rigorosa gestione e attenzione all’intero processo con riflesso diretto sui prodotti e sulla loro qualità che, da qualche anno, garantita anche dalla loro perfetta pulizia e decontaminazione: un lavaggio efficace, performante ed ecosostenibile ottenuto grazie all’impiego di una lavatrice sottovuoto ad alcoli modificati KP.Max 600 Decor della IFP Europe di Galliera Veneta (PD).
Il valore aggiunto della tecnologia ad alcoli modificati
Fino a dicembre 2016, Sariv ha utilizzato per il lavaggio delle minuterie prodotte un impianto di lavaggio ad acqua, con annesso impianto di depurazione. «Fino a una notte di metà dicembre – ricorda l’ing. Sartore – quando nello stabilimento un corto circuito ha innescato un incendio, che in pochissimo tempo ha distrutto l’impianto di zincatura e, appunto, l’impianto di lavaggio ad acqua e quello di depurazione». Un evento che ha suscitato in azienda più di una riflessione. Non ultima, quella riguardante per esempio l’aspetto economico da affrontare per ristabilire l’impianto di zincatura, visto che le aggiornate normative avrebbero obbligato a effettuare interventi di adeguamento con ingenti investimenti necessari. «Non solo – prosegue l’ing. Sartore – a questo aspetto si è aggiunto anche il non meno importante e costante nostro impegno nelle politiche ambientali e nell’attenzione per la salute dei nostri dipendenti. Anche per questo motivo la decisione presa è stata non solo quella di rinunciare al ripristino dell’impianto di zincatura al nostro interno, affidandoci sin da subito a partner esterni, ma anche quella di trovare un’alternativa più sicura, ecologica, e meno energivora, per soddisfare le esigenze di lavaggio dei componenti da noi prodotti».
Dopo una ricerca di mercato, Sariv individua così nella tecnologia ad alcoli modificati di IFP Europe la risposta ideale alle proprie esigenze, in quanto avrebbe consentito di assicurare il grado di pulizia e decontaminazione attesi, di ridurre drasticamente il consumo di liquido di lavaggio, oltre ad abbattere i tempi ciclo e la potenza utilizzata dall’impianto.
Decontaminazione e asciugatura perfetta per piccole e grandi quantità di prodotto
Finalizzata nel corso del 2017, l’installazione del nuovo impianto di lavaggio IFP ha permesso all’azienda di Fontaniva non solo di soddisfare questa specifica fase di processo, ma anche di ottimizzare e migliorare in alcuni casi le successive. «Mi riferisco per esempio al trattamento termico – conferma l’ing. Sartore – nel quale, la presenza di piccoli residui d’olio rimasti dopo il lavaggio sui componenti, in precedenza avrebbe comportato problemi in termini di qualità, a seguito di possibili bruciature, richiedendo poi interventi aggiuntivi. Criticità risolta grazie dal nuovo impianto. In più sottolineerei che l’efficacia del processo di disoleazione e il grado di pulizia ottenibile avevano dei livelli per noi in precedenza praticamente impossibili da raggiungere».
Non a caso la gamma di lavatrici KP Kleen Power di IFP Europe, il cui cuore tecnologico è lo stesso della KP.MAX 600 versione Decor scelta da Sariv, si rivela perfetta per il trattamento di qualsiasi tipo di prodotto, anche costituito da metalli diversi tra loro, sia in piccole che grandi quantità da trattare, di qualsiasi dimensione e complessità strutturale, contaminato da acqua, oli e scarti di lavorazione. Tutti i cicli di lavaggio vengono effettuati interamente in sottovuoto con l’impiego di ultrasuoni, di soluzioni detergenti acquose, alcoli modificati, idrocarburi o idrocarburi HFE. Ovvero un sistema che garantisce una decontaminazione e asciugatura perfetta delle superfici metalliche, con un livello idoneo anche per i requisiti richiesti dalla normativa Moca (riguardante i materiali e gli oggetti destinati al contatto con gli alimenti). In aggiunta, KP Kleen Power garantisce un significativo risparmio energetico, un recupero del 99% degli elementi contaminanti in linea con le disposizioni in tema di Economia Circolare, totale assenza di sversamenti di morchie o altri componenti nocivi e soprattutto assicura la massima sicurezza per l’operatore.
Produzione tracciata e certificata
Come già menzionato, Sariv produce circa 3 milioni di pezzi al giorno, grazie a un parco macchine comprendente una quarantina di stampatrici, una decina di chiodatrici e una trentina di assemblatrici. Tecnologie che permettono di lavorare materiali diversi (alluminio, acciaio, inox, rame e cupronickel), per ottenere componenti stampati da filo aventi dimensioni comprese tra 2,4 e 8 mm di diametro, per lunghezze comprese tra 5 e 50 mm. Minuterie suddivisibili per tipologia in: rivetto a strappo standard, sistema di fissaggio formato da due parti assemblate tra loro, ovvero la boccola e il chiodo; rivetto a strappo speciale; rivetto a strappo strutturale; inserto filettati. Si aggiungono poi per l’applicazione dei rivetti a strappo, anche tre tipologie di rivettatrici manuali e due rivettatrici oleopneumatiche. «La nostra sfida – commenta l’ing. Sartore – è quella di offrire servizi di ingegnerizzazione di prodotto per fornire la soluzione ideale per ogni applicazione. Un produzione custom che richiede, per essere altamente competitiva, anche la progettazione e realizzazione dell’attrezzatura necessaria per la produzione e l’ingegnerizzazione del processo. Tutte attività svolte dal nostro dipartimento tecnico». Tutte le fasi produttive vengono svolte internamente a Sariv e sono conformi ai requisiti della norma per i sistemi di gestione qualità UNI EN ISO 9001:2015; dal 2018 l’azienda dispone inoltre certificazione IATF 16949:2016 (standard internazionale dei sistemi di gestione qualità nell’industria automobilistica); nel 2020 sono invece state acquisite le certificazioni ISO 14001:2015 e ISO 45000:2018, rispettivamente in riferimento al sistema di Gestione Ambientale e al Sistema di Gestione della Salute e Sicurezza sul Lavoro. «La peculiarità che ci distingue sul mercato – continua l’ing. Sartore – è quella di poter riuscire sempre a risolvere il problema di fissaggio partendo anche direttamente dall’applicazione finale. In questo modo possiamo fornire la miglior soluzione possibile. Il laboratorio tecnico interno permette il controllo di ogni caratteristica dimensionale e meccanica dei prodotti, tramite attrezzatura come macchine a trazione, misuratori ottici elettronici, e misuratori di durezza. Disponiamo inoltre di un reparto di selezione tramite telecamere per poter fornire prodotti con PPM 50, con la possibilità di poter raggiungere nel breve, grazie a nuovi investimenti in macchinari effettuati, anche produzioni a scarto zero». L’azienda è in ogni caso in grado di fornire per ogni produzione tutti i documenti necessari alla certificazione di prodotto per l’automotive, da PPAP a IMDS, a VDA. «Ogni singola fase, lavaggio pezzi incluso – sintetizza l’ing. Sartore – dello svolgimento del processo, è tracciata dal nostro sistema MES, in modo da avere uno storico completo di ogni lotto di produzione. Grazie a tutto ciò, siamo in grado di fornire i nostri prodotti ai clienti più esigenti, tra i quali annoveriamo anche tutti i maggiori costruttori di automobili europei».
Performanti, efficienti e anche belle da vedere
Dei 3 milioni di pezzi prodotti al giorno, non meno dei due terzi necessita in Sariv di un lavaggio, con lotti di stampaggio che partono generalmente da circa 50mila pezzi. «Una parte decisamente significativa – conclude l’ing. Sartore – e che ben denota l’importanza, all’interno del nostro flusso, del nuovo impianto acquisito da IFP Europe. Integrazione che ha portato con sé più di un beneficio operativo. Prima di tutto ha garantito una qualità dei lavaggi, come già menzionato, di assoluto livello, assicurando anche la ripetibilità costante del processo di pulizia e di decontaminazione dei componenti. Senza più la necessità, come accadeva in alcuni casi col precedente sistema, di rilavorazioni di disoleazioni in quanto non soddisfacenti i requisiti attesi. Altrettanto apprezzata è l’efficienza del processo che ha portato a una diminuzione dei costi, grazie a contenuti consumi energetici e di acqua, oltre che per lo smaltimento dei residui, praticamente nullo».
A questo proposito, la distillazione e la filtrazione continua degli alcoli modificati e idrocarburi utilizzati per il lavaggio e la finitura della componentistica metallica da trattare (con l’ausilio di filtri che permettono la separazione completa dell’olio dai liquidi di lavaggio e la separazione delle emulsioni dall’acqua con scarico automatico in continuo), permettono il totale recupero della limatura metallica asciugata e deodorata già nel filtro, e il recupero del 99% degli oli emulsionanti presenti nel prodotto da trattare. «Da considerare anche – conclude l’ing. Sartore – l’importante recupero di spazio utile produttivo, visto che l’impianto IFP occupa circa un quinto di quello prima necessario, con anche un design e una grafica estetica che permette di rendere l’ambiente di lavoro più gradevole».
MASSIMA QUALITÀ DI LAVAGGIO, ANCHE NELLE APPLICAZIONI PIÙ IMPEGNATIVE
L’eco-sostenibilità rappresenta uno dei principi fondanti che sono alla base della filosofia produttiva di IFP Europe. Approccio che si esplica in una tecnologia capace di effettuare performanti lavaggi sottovuoto, impiegando liquidi a basso impatto ambientale ad alcoli modificati, garantendo il massimo delle prestazioni con notevoli vantaggi. L’intera linea KP Kleen Power resa disponibile dal costruttore è configurata con componentistica di alta qualità che permette di ottenere risultati sorprendenti di processo, qualunque sia il grado di contaminazione e la tipologia dei componenti metallici da trattare, anche in caso di foratura cieca profonda. Prerogative che caratterizzano anche la linea KP.Max, cui appartiene l’impianto scelto da Sariv (nella versione KP.Max 600 Decor), indicata per il trattamento di volumi produttivi molto elevati, partendo da carichi singoli dalle dimensioni importanti. Ideale per materiale sottoposto a trattamento termico, questa lavatrice sottovuoto si distingue per accogliere carichi fino a 600 kg e dimensioni fino a 600 x 1.000 x 600h mm, riuscendo a effettuare mediamente 3 ÷ 6 cicli/ora. Numeri di cicli, questi, comuni anche per i modelli KP.Max 400 (per carichi fino a 400 kg e dimensioni fino a 1.200 x 450 x 300h mm) e KP.Max 800 (fino a 800 kg per 800 x 1.200 x 800h mm).
Cosa dicono di noi sulle testate di settore
Di seguito alcuni articoli, realizzati da nostri clienti, in cui vengono descritte le caratteristiche delle loro attività e come l’utilizzo dei nostri impianti di lavaggio sottovuoto contribuiscono alla realizzazione qualitativa dei loro prodotti.