ipcm® Industrial Cleaning Technologies
N.17 – 2020 FEBRUARY
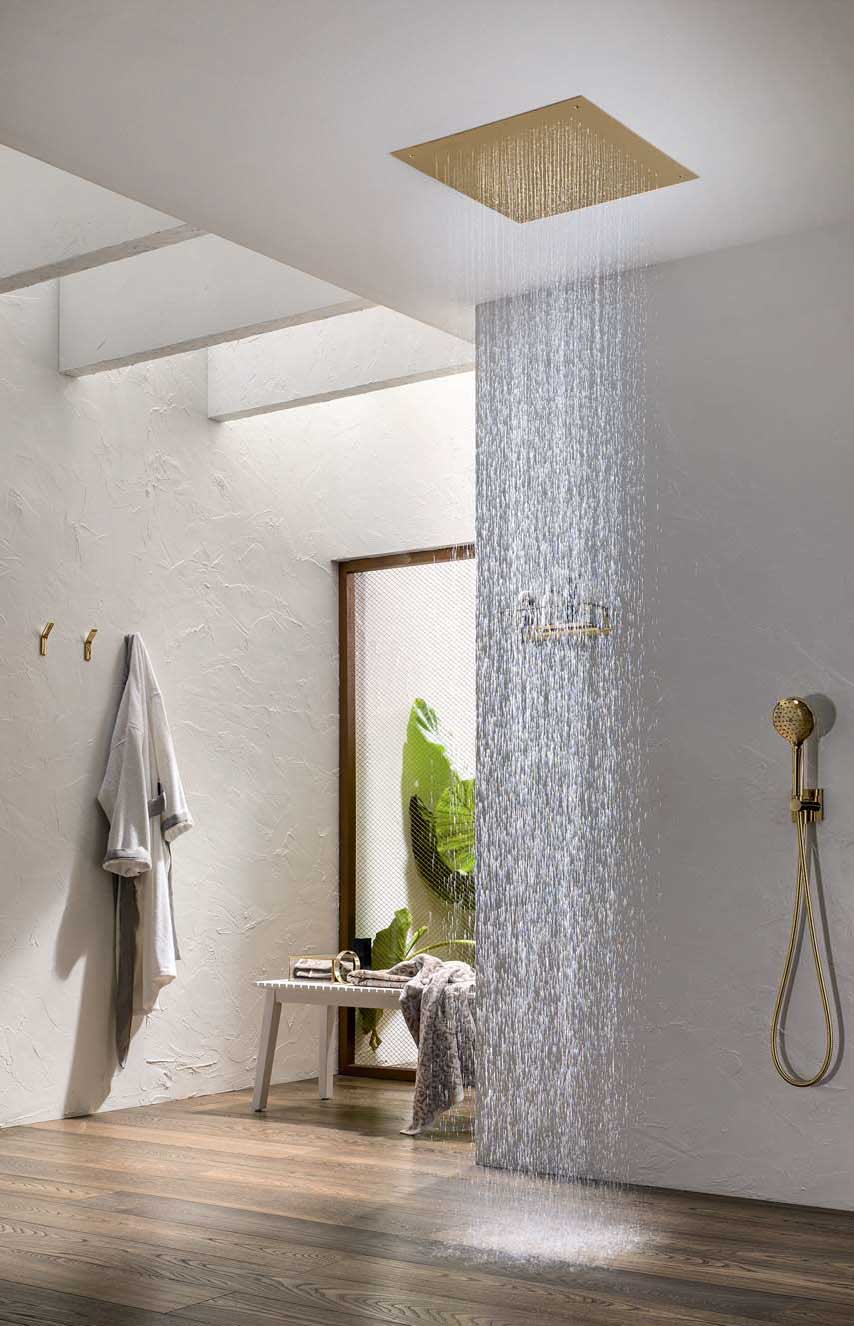
Scarica l’articolo completo in formato PDF
Il valore aggiunto del lavaggio per i componenti di sistemi doccia d’alta gamma cromati in PVD
Il Bello e Ben Fatto è l’espressione più facilmente riconoscibile del Made in Italy. Almar, società specializzata nella produzione di sistemi doccia per l’arredo bagno, è una delle aziende che contribuiscono, con la qualità dei propri prodotti, all’aff ermazione del Made in Italy nel mondo. Per la pulizia dei componenti dei propri sistemi doccia, Almar ha scelto una macchina di lavaggio sottovuoto ad alcoli modifi cati di IFP Europe in grado di garantire la rimozione completa dei contaminanti prima dell’applicazione del coating estetico con tecnologia PVD.
Nel rapporto “Esportare la dolce vita” realizzato dal Centro Studi di Confindustria per il Summit 2019 troviamo una definizione dettagliata del concetto di “Bello e Ben Fatto (BBF)”, diff uso da qualche anno nell’industria del lusso italiana: “Il BBF racchiude in sé tutti quei beni che rappresentano l’eccellenza italiana in termini di design, cura, qualità dei materiali e delle lavorazioni. Si tratta di prodotti che si distribuiscono in tutti i comparti produttivi, ma che trovano la loro massima espressione nelle produzioni più legate al gusto e alla creatività.
Leggi di più
Da questo punto di vista il BBF è l’espressione più facilmente riconoscibile del Made in Italy, riprendendo i tratti più caratteristici dell’heritage culturale dell’Italia, delle sue tradizioni, dei suoi paesaggi e delle opere d’arte, e contribuendo a comporre l’immagine dell’Italia produttiva”.
Molte delle aziende che hanno contribuito e contribuiscono tuttora all’aff ermazione del Made in Italy nel mondo presentano una storia di attività famigliare fortemente ancorata al territorio che le ha viste nascere e svilupparsi. Si tratta di società che attraverso la cura del più piccolo dettaglio e investimenti oculati hanno saputo crearsi uno spazio in un settore di diffi cile penetrazione come quello dei beni di consumo di alta fascia.
Almar, società specializzata dal 1996 nella produzione di sistemi doccia per l’arredo bagno, è una di queste.
“La società fondata da mio fratello e dal sottoscritto” – racconta Marco Civelli, titolare insieme ad Aldo di Almar Srl – affonda le proprie radici nell’azienda fondata alla fi ne degli anni
Sessanta da nostro padre Gianluigi, e dedicata dapprima alla costruzione degli stampi per il settore termoplastico e allo stampaggio a iniezione.
Nel 1996 abbiamo rilevato una delle società da cui nostro padre si riforniva, e presso cui mi sono formato professionalmente. Qui ho avuto la possibilità di seguire l’intero ciclo produttivo di componenti per manufatti termoplastici, dalla progettazione alla costruzione degli stampi ad essi dedicati. Questo ha rappresentato il primo nucleo dell’azienda attuale”.
Nel 2000 Almar trasferisce la propria attività nell’attuale stabilimento di Gavirate, con un organico di una decina di collaboratori dedicati allo stampaggio ad iniezione e all’attrezzeria per la costruzione degli stampi. “Oggi l’organico complessivo è arrivato a 100 unità. Poi grazie alla creazione e al rapido sviluppo del nostro ufficio tecnico” – prosegue Civelli – “abbiamo iniziato a realizzare manufatti frutto della nostra creatività, iniziando dapprima con componenti termoplastici di piccole dimensioni, per poi ampliare il nostro portfolio prodotti con anche componentistica in ottone e in acciaio.
Da qui abbiamo realizzato un reparto interno di assemblaggio e collaudo, per poter curare internamente tutto il ciclo di produzione dei nostri prodotti. L’evoluzione è stata tale per cui alla fine della prima decade degli anni Duemila abbiamo avuto l’esigenza di costruire un secondo stabilimento, con sede a Cocquio Trevisago, a poca distanza dal primo, trasferendo in questa sede le lavorazioni di Costruzione Stampi e Stampaggio termoplastico a iniezione.
Nel 2015 abbiamo internalizzato la lavorazione della lamiera in acciaio, dotandoci di macchine tecnologicamente avanzate per il trattamento dell’acciaio inox.
Infine, due anni fa abbiamo introdotto il sistema PVD per la realizzazione del coating estetico, per far fronte al picco di domande di componenti dell’arredo bagno con finiture speciali come, per esempio, gli effetti dorati e ramati. Da quel momento è subentrata però anche l’esigenza di risolvere le problematiche di contaminazione dei pezzi, prima che venissero rivestiti con trattamento PVD. Abbiamo quindi iniziato una ricerca tra i produttori di impianti di lavaggio per trovare la miglior soluzione per le nostre necessità. Dopo un’attenta analisi, la scelta è ricaduta sull’impianto KP MAX 600 di IFP Europe, società di Galliera Veneta (Padova) specializzata nella progettazione, costruzione e installazione di impianti di lavaggio ad alcoli modificati e idrocarburi”.
L’attenzione al dettaglio di Almar: dalla cura del prodotto alla scelta dei fornitori
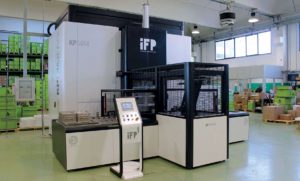
L’impianto di lavaggio KP MAX 600 di IFP Europe.
La parola d’ordine di Almar per la realizzazione delle proprie soluzioni d’arredo bagno è ‘perfezione’.
“Per la nostra clientela i requisiti fondamentali sono ‘qualità’ e ‘servizio’ – conferma Civelli. I nostri manufatti sono distribuiti in tutto il mondo con 3 modalità diff erenti: sul mercato italiano, ai produttori di rubinetterie e box doccia volumi produttivi elevati e dimensioni e conformazioni molto variabili.
Abbiamo quindi richiesto a IFP Europe di fornirci un impianto in grado di lavare fino a 12 cestelli standard contemporaneamente. I cestelli possono essere sostituiti da altri di formato più grande grazie al telaio del vassoio studiato ad hoc per le nostre necessità: i nostri pezzi possono raggiungere dimensioni massime di 70×90 cm”.
“Nel caso di Almar – precisa Sabbadin – la durata standard del ciclo è di circa 20 minuti, variabili in base alla tipologia di sporco da rimuovere.
Ulteriori parametri modifi cabili in base alle esigenze di lavaggio sono l’utilizzo o meno degli ultrasuoni e del movimento basculante del cestello, oltre alla temperatura e al tempo di permanenza dei manufatti all’interno della camera di lavaggio”.
“Una delle problematiche principali che abbiamo sottoposto a IFP Europe – prosegue Ferri – era l’efficacia del lavaggio per ogni singolo manufatto, ma con la possibilità di gestire più tipologie di prodotto impostando la stessa sequenza di cicli. Abbiamo infatti realizzato uno studio per capire quale sequenza di lavaggio per la rimozione dei 3 contaminanti principali fosse che acquistano i nostri componenti per completare i loro sistemi; sul mercato europeo abbiamo un’ampia rete di distributori-grossisti che rivendono i nostri prodotti con il loro marchio e in parte con marchio Almar; a livello internazionale in alcuni Paesi, come gli Stati Uniti e nel Medio ed Estremo Oriente e Sud Africa, vendiamo prodotti a marchio Almar in showroom e negozi.
Nel complesso il mercato estero rappresenta il 65% della nostra produzione”.
“Il nostro obiettivo principale – interviene Mirco Ferri, Purchasing Manager di Almar – è quello di proporre al mercato prodotti ‘perfetti’ sotto ogni punto di vista, in particolare estetico e funzionale. Questo è il motivo per cui nel corso degli anni abbiamo puntato all’insourcing delle principali lavorazioni. Abbiamo notato un aumento delle esigenze qualitative del mercato con tempi di consegna molto stretti, e il solo modo per farvi fronte è stato quello di assicurarsi il controllo dell’intero ciclo produttivo; un vantaggio non solo in termini qualitativi, ma anche quantitativi e temporali”.
La stessa cura del dettaglio che Almar applica alle proprie realizzazioni si riflette anche nella scelta dei propri fornitori. “Non ci accontentiamo di instaurare un mero rapporto di compravendita con i nostri partner – continua Ferri. Nella scelta dei collaboratori, a partire dai fornitori dei materiali fi no a quelli delle macchine e attrezzature utili alle nostre lavorazioni, la questione dei costi è importante, ma secondaria: vogliamo innanzitutto collaborare con aziende che non solo ci forniscono un prodotto di qualità, ma con cui anche poter costruire un rapporto di interazione e condivisione stabile e duraturo. In particolare, cerchiamo sempre collaboratori che ci mettano a disposizione il proprio know-how, per farlo nostro e migliorare i processi costruttivi e quindi i prodotti. Così è stato anche per la scelta del fornitore dell’impianto di lavaggio: oltre alla qualità del prodotto selezionato, abbiamo instaurato con lo staff tecnico di IFP un rapporto solido, iniziato con una fase preliminare di test per verificare che la soluzione di lavaggio proposta fosse adatta alle nostre esigenze”.
Un impianto di lavaggio funzionale ad un sistema produttivo complesso
Per la produzione dei sistemi doccia, Almar tratta componenti di materiali diversi, in acciaio inox, ottone, alluminio, resine termoplastiche, tecnopolimeri e ABS.
L’intervento di lavaggio risulta fondamentale per tutti i componenti destinati al trattamento nell’impianto PVD.
“Il ricevimento del materiale – spiega Ferri – è diversifi cato in base alla sua provenienza. Il prossimo punto in agenda del nostro programma di internalizzazione prevede l’integrazione all’interno dell’azienda del reparto di torneria per la produzione di piccoli lotti. Attualmente riceviamo i componenti da barra tornita, in ottone e acciaio, da fornitori esterni.
Qui la problematica è determinata dalle paste di pulitura utilizzate per la lucidatura, che possono inquinare i trattamenti superfi ciali. Un’altra criticità deriva dalle lavorazioni eseguite internamente con l’acciaio inox supermirror AISI 304 e 316: oltre ai residui di olio ed emulsioni delle lavorazioni meccaniche, il taglio laser di questa tipologia di materiale provoca una bruciatura della pellicola protettiva che contamina la superficie. Le prove effettuate presso la sede di IFP hanno dimostrato che l’impianto di lavaggio è in grado di rimuovere anche questa tipologia di morchia. L’impianto deve essere in grado poi di lavare i manufatti in ottone che devono poi essere sottoposti alla verniciatura o al trattamento galvanico, lavorazioni che gestiamo in outsourcing. Infine, alcuni nostri clienti ci inviano prodotti di loro realizzazione da rivestire in PVD , da abbinare ai nostri articoli. Anche questi pezzi devono essere sottoposti al lavaggio pre-PVD. La contaminazione delle superfici con olio, emulsioni e paste di lucidature era la principale problematica da risolvere per ottenere un rivestimento duraturo e senza difetti”.
Le caratteristiche dell’impianto di lavaggio KP MAX 600
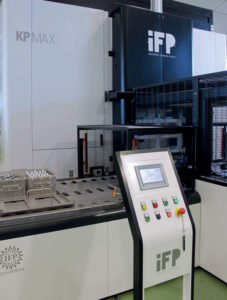
L’impianto è studiato per off rire ergonomia e facilità di accesso agli operatori.
Il sistema di lavaggio scelto da Almar fa parte della serie KP Kleen Power.
“Grazie al ciclo di trattamento interamente sottovuoto fi no a 1 millibar – precisa Giacomo Sabbadin, Direttore Generale di IFP Europe – e alla ricca dotazione di serie e opzionale, la macchina installata rappresenta una delle migliori tecnologie di lavaggio presenti attualmente sul mercato.
Nella versione MAX gli impianti permettono il massimo dei risultati nelle applicazioni più impegnative per volumi di produttività richiesta e contaminazione presente. Il sistema, funzionante completamente in vuoto, è caratterizzato da filtrazione e distillazione continua del liquido di lavaggio, separazione continua dell’emulsione con scarico automatico dell’acqua e separazione completa dell’olio dal liquido di lavaggio, con scarico automatico in continuo”.
“Data la varietà dei prodotti che trattiamo – continua Ferri – abbiamo funzionale alle nostre lavorazioni, allo scopo di evitare che il liquido venisse
contaminato in modo eccessivo, nonostante la distillazione continua.
Oltre alla flessibilità dei cicli di lavaggio e ai risultati qualitativi sulla superficie di manufatti diversi per caratteristiche e materiale, la soluzione di IFP Europe ci ha convinto perché si allinea perfettamente alla visione aziendale di un ambiente di lavoro pulito e confortevole per gli addetti ai diversi reparti, e per il design lineare e pulito della macchina, che ben si adatta al nostro concept di prodotto”.
Conclusioni
In Almar, l’analisi delle migliori soluzioni per il lavaggio dei propri componenti è ancora all’ordine del giorno.
“Siamo continuamente alla ricerca della perfezione dei nostri prodotti – conclude Civelli – e il lavaggio dei componenti prima della finitura superficiale è diventato uno stadio fondamentale dell’intero processo produttivo. Infatti stiamo valutando di introdurre un altro impianto IFP Europe nell’altro stabilimento dove sarà avviato il reparto di torneria, per evitare l’eventuale contaminazione dei pezzi. Sempre allo scopo di evitare la permanenza di eventuali residui o impronte sulla superficie dei manufatti, stiamo studiando con il team tecnico di IFP la costruzione di telai speciali, che, dopo il lavaggio, possano entrare direttamente nell’impianto di rivestimento PVD. Per ottenere la perfetta pulizia, nessun dettaglio può essere lasciato al caso”. Una filosofi a che rispecchia appieno il concetto di Bello e Ben Fatto che caratterizza i prodotti Made in Italy di maggior successo a livello internazionale.
Cosa dicono di noi sulle testate di settore
Di seguito alcuni articoli, realizzati da nostri clienti, in cui vengono descritte le caratteristiche delle loro attività e come l’utilizzo dei nostri impianti di lavaggio sottovuoto contribuiscono alla realizzazione qualitativa dei loro prodotti.