n.85 – Gennaio – Febbraio – Marzo 2016
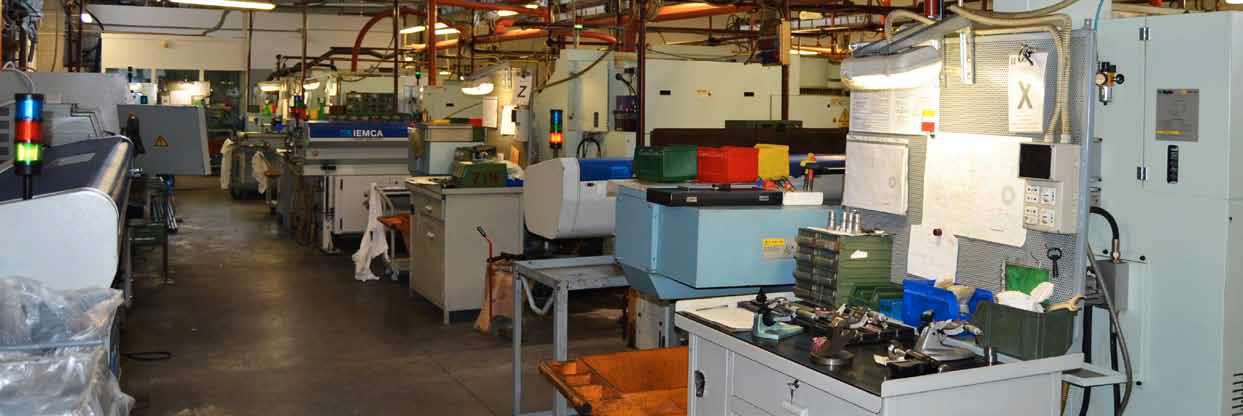
Scarica l’articolo completo in formato PDF
NUOVA TORNERIA ZANOTTI
Ritorno al futuro: dall’acqua al solvente
L’evoluzione delle tecnologie di lavaggio negli ultimi decenni è stata fortemente condizionata dai parametri ambientali, che hanno spostato il mercato verso alcuni prodotti, a seconda delle emergenze del momento. In passato ciò che contava era solo l’efficacia del ciclo e la sua economicità, per cui i solventi hanno rappresentato per vari decenni la soluzione ottimale e quindi la più diffusa. Le tematiche ecologiche emerse negli anni ’80 hanno introdotto un importante riflessione sui costi ambientali della produzione industriale, portando a valutare con attenzione l’impatto ambientale delle diverse tecnologie, che da quel momento sono state giudicate non solo per le loro prestazioni tecniche ed economiche.
Read more
La carenza di informazioni tecnico-scientifiche ha però lasciato spazio ai cosiddetti “prodotti ecologici”, promossi con intenti puramente commerciali, sfruttando gli allarmismi che l’attualità proponeva di volta in volta. A seconda del periodo storico sono quindi stati proposti prodotti che riducevano l’impatto energetico, altri che evitavano il buco dell’ozono, altri ancora che riducevano l’effetto serra e così via. Solo negli ultimi anni le aziende hanno cominciato ad analizzare i cicli di produzione in modo razionale, tenendo conto di tutti i fattori economici, prestazionali e ambientali, senza farsi condizionare da mode o luoghi comuni. Il caso della Nuova Torneria Zanotti SRL rappresenta uno degli esempi più concreti di questa nuova visione imprenditoriale applicata al lavaggio, in cui si fa tabula rasa del passato, superando abitudini cristallizzate e analizzando tecnicamente le proprie esigenze produttive, così da poter scegliere prodotti e macchine efficaci, produttive e ambientalmente compatibili
L’azienda
La Nuova Torneria Zanotti è un’azienda emiliana radicata nel territorio, in cui opera dal 1966, specializzata nella produzione di particolari meccanici di alta precisione per industrie di vari settori, quali la pneumatica oleodinamica, la minuteria di precisione, l’elettromedicale e molti altri. L’azienda lavora in un’area complessiva di circa 3.000 metri quadrati e dispone di macchinari ad alta tecnologia, tra cui 36 torni a controllo numerico con caricatori a barra, a fantina fissa e mobile, con speciali attrezzature personalizzate che consentono di produrre articoli di alta qualità, rispondenti alle esigenze dei singoli clienti. L’azienda, che dispone di impianti di lavaggio, pallinatura, lappatura, si occupa della fornitura del particolare finito di rullatura, rettifica, trattamenti termici, trattamenti superficiali, ecc., provvedendo anche a effettuare montaggi, con specializzazioni su componenti oleodinamici.
Particolare attenzione è dedicata alla selezione dei sub-fornitori, affinchè i lavori dei trattamenti termici e galvanici loro affidati siano eseguiti con precisione e garanzie di qualità. I vari comparti dell’azienda (tecnico, produttivo, commerciale, amministrativo) operano in piena sintonia; ne consegue una gestione efficiente e moderna, capace di rispondere alle esigenze di una larga e differenziata clientela.
La Nuova Torneria Zanotti non è soltanto in grado di fornire una vasta gamma di lavorazioni che portano al prodotto finito; offre anche, come valore aggiunto, la propria esperienza, frutto di quasi cinquant’anni di lavoro caratterizzato da passione, dedizione, professionalità e serietà.
Sono questi i principi e i valori che hanno consentito e che consentiranno sempre di garantire organizzazione, preparazione, affidabilità e massima disponibilità.
La società è certificata ISO 9001, garanzia non solo di qualità del prodotto, ma anche dell’efficienza del sistema di gestione dell’azienda e dispone di adeguate strumentazioni di controllo e collaudo, unite ad un rigoroso metodo operativo per la verifica tecnica e qualitativa dei particolari come rugosità, durezza, controllo profili, rotondità, concentricità, ecc.
Il ciclo produttivo
L’azienda emiliana è specializzata in particolare nel settore oleodinamico, nel quale ha raggiunto altissimi livelli di qualità nella produzione di sedi, valvole, cartucce, steli, alberini, tappi, spilli e ogni altro componente oleodinamico, pneumatico ed idraulico.
Le macchine consentono di di lavorare tutti i tipi di materiale tra cui: AVP, AVZ, PR 80, 16CrNi4, 16Cr- Ni4Pb, 18CrMo5, 42CrMS4, 18CrMo5, 42CrMS4, Alluminio 11s, Ottone, Inox Aisi 303, ETG 88, ETG 100. Oltre ai materiali più comuni, vengono lavorati, sempre da barra, PVC, Teflon, Ergal, oltre altre leghe di acciai rame, bronzo e ghisa.
Il lavaggio
Vittorino Romagnoli, socio e direttore tecnico generale dell’azienda, e Andrea Ranaldi, responsabile dell’impianto di lavaggio, ci hanno spiegato il percorso che ha portato alla scelta dell’attuale sistema di lavaggio
“In un mercato in rapida evoluzione – ci ha detto Romagnoli – in cui reattività, disponibilità competenza e versatilità sono requisiti irrinunciabili, la nostra azienda negli ultimi anni ha avviato un processo di innovazione, investendo molto nella formazione e nella specializzazione del personale, coinvolto in modo diretto nella gestione dell’attività produttiva, in quanto consideriamo tutti gli operatori come il vero motore e la principale risorsa strategica per il presente ed il futuro aziendale.
In questo processo è rientrata anche una revisione dei cicli di lavaggio, a cui in passato abbiamo dato meno importanza rispetto alle altre lavorazioni, considerandola un’attività accessoria e quasi improduttiva.
Per oltre 20 anni abbiamo utilizzato una lavatrice a immersione con insufflaggio dell’aria e un’altra con cestello a spruzzo, in cui gli agenti di lavaggio erano detersivi alcalini in soluzione acquosa, a cui faceva seguito l’applicazione di passivanti antiruggine, in quanto l’asciugatura non era mai completa.
Sull’onda della consuetudine per anni abbiamo sorvolato su alcune imperfezioni del processo acquoso (presenza di residui di contaminante, asciugatura incompleta), ma poi la clientela è diventata sempre più esigente, rifiutando i particolari con presenza di anche minime tracce di ossidazione (che nonostante l’applicazione del passivante, non riuscivamo a eliminare completamente) e pretendendo gradi di lavaggio sempre più spinti.
La globalizzazione ha accentuato la competitività, imponendo livelli qualitativi elevati, a costi ridotti. Sempre più aziende assegnano ai fornitori un punteggio annuale sulla qualità del prodotto e del servizio offerto, per cui per noi gli esami non finiscono mai.
La necessità di una perfetta pulizia ha indotto numerosi nostri clienti a introdurre sempre più spesso una verifica analitica sulla quantità e la qualità dei residui di contaminanti presenti sui pezzi; qualcuno poi ha cominciato a imporre la conformità a tolleranze di lavaggio che prima venivano richieste solo sui requisti meccanici di lavorazione, per cui varie volte abbiamo dovuto effettuare operazioni di pulizia manuale supplementari, dopo il lavaggio in macchina.
Le nostre lavorazioni di torneria, che precedono il lavaggio, sono caratterizzate dall’impiego di numerosi tipi di contaminanti (oli da taglio, interi e emulsionabili, utilizzati come lubrorefrigeranti). Le difficoltà maggiori derivano però dalla necessità di asportare i vari tipi di oli utilizzati dai nostri fornitori per la lavorazione del materiale che impieghiamo; si tratta infatti di oli e grassi dei quali non conosciamo la natura chimica e sui quali non possiamo agire alla fonte per eventuali sostituzioni, anche quando sono particolarmente difficili da lavare. Ciò rende molto difficoltosa l’individuazione di uno specifico detergente in grado di essere efficace per tutti i contaminanti. Dopo varie prove abbiamo quindi optato per un solvente “universale” a basso impatto ambientale, il DOWCLENETM 1601, un prodotto a base di alcoli modificati studiato da Dow Chemical, fornitoci dalla società Brenntag. In questo passaggio dall’acqua al solvente ci è stato molto utile il servizio di “Solvent Training” fornito da Dow Chemical, che ci ha accompagnato nel processo di formazione degli addetti e che tuttora ci fornisce un’accurata assistenza tecnica.
Il prodotto ha un elevato potere solvente per oli e grassi ed è quindi efficace nel rimuovere la svariata gamma di contaminanti che caratterizza la nostra produzione. La qualità migliore del DOWCLENETM 1601, secondo me, consiste nella capacità di evaporare completamente, senza lasciare residui, per cui i pezzi sono perfettamente asciutti e possono essere manipolati e stoccati senza alcuna protezione antiruggine. Il prodotto ci ha consentito di migliorare radicalmente la qualità del lavaggio, mantenendo la produttività e la flessibilità delle nostre lavorazioni, nel pieno rispetto degli standard di sicurezza nell’ambiente di lavoro e di emissioni verso l’esterno, che hanno sempre contraddistinto la nostra attività.
L’ultima fase di questo processo di ottimizzazione sarà l’utilizzo del sistema SAFE-TAINERTM, attualmente limitato alla fornitura, stoccaggio e manipolazione del solvente, che verrà utilizzato anche per lo smaltimento dei rifiuti, in modo da rendere l’intera fase del lavaggio a ciclo chiuso.
Per raggiungere questo risultato abbiamo installato una macchina di ultima generazione, caratterizzata dal ciclo di trattamento sottovuoto, fornita da IFP, che abbiamo scelto vista l’esperienza maturata in questi anni, con decine di realizzazioni impiantistiche di questo tipo.
La KP 100 con ultrasuoni ci consente di lavare 8 cestelli/ ora (ogni cestello contiene circa 25 kg di pezzi), con un consumo di 200 litri/anno di solvente, che in questo primo anno di impiego ha richiesto solo un controllo mensile del ph e dell’acidità, che effettuiamo mediante il kit in dotazione.
La manodopera impiegata per le operazioni di lavaggio è rimasta invariata e stiamo valutando l’opportunità di automatizzare le operazioni di carico e scarico dei cestelli”.
IMPIANTO DI LAVAGGIO IFP KP 100
Dati tecnici | Dimensioni carico: 600x450x200h | Peso carico: kg 100 | Ingombro mm: 1800x2000x2600h | Cicli/ora: 4-8 |
Dotazione di serie | Costruzione completamente in inox – Impiantistica a tenuta di vuoto – Pompe spruzzatura ad alta pressione – Pompe vuoto – Sistema abbattimento criogenico – Distillatore strippaggio morchie – Sistema ermetico di carico/scarico solvente – Filtrazione solvente – Doppio serbatoio di stoccaggio solvente – Pannello operativo touch screen – Teleassistenza via internet | |||
Dotazione opzionale | Trasduttori ultrasonori – Terzo serbatoio solvente – Gruppo applicazione agente protettivo – Gruppi filtrazione supplementare – Sistemi automatici di movimentazione carichi – Sistemi di riconoscimento automatico carichi – Utilizzo solventi clorurati | |||
Applicazioni | Minuteria meccanica tornita – Minuteria meccanica di precisione – Minuteria metallica stampata – Pressofusioni – Particolari piegati – Componenti oleodinamici – Valvolame – Raccorderia – Rubinetteria – Scambiatori di calore – Automotive – Componenti sinterizzati – Ingranaggeria – Posateria – Pentolame – Orologeria – Oreficeria – Medicale |
WHAT THEY SAY ABOUT US
Below are some articles written by our customers and published in the sector publications, describing their activities and how their use of our vacuum washing equipment contributes to the quality of their products.