N. 14 – 2018 OCTOBER
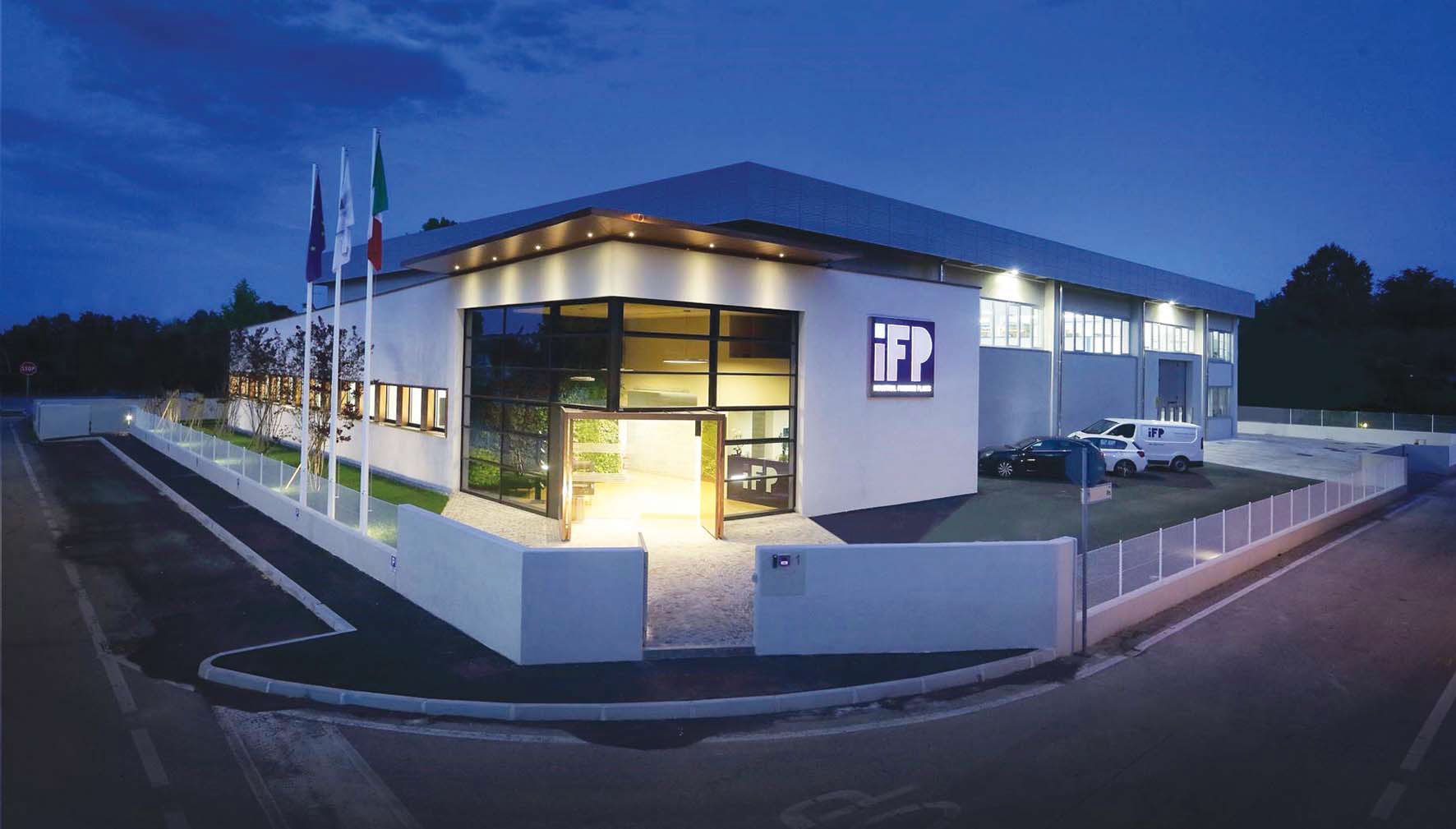
Download the full news in PDF
Eco-friendly cleaning plants: IFP Europe’s key to success
Read more
IFP Europe was established 8 years ago by a team of engineers with in-depth experience in the industrial cleaning field. The company has managed to establish itself as a sector leader in a very short time. In June, it inaugurated a new 3,000 m2-wideheadquarters, thus doubling its covered surface and improving all the departments involved in the construction its washing machines, from design to production, up to the automated warehouse. “Our plant expansion has helped us improve our production organisation,” states IFP Europe General Manager Giacomo Sabbadin, “in terms of space available, in which it is now possible to produce a greater number of large-sized plants, of safety guaranteed during construction operations, and of ease of cleaning.”IFP’s goal is to launch new, increasingly reliable machines that ensure reduced cleaning times and ever-higher quality. “That is why we have improved our technical department for the design of new systems and integrated our test area with 8 fully equipped stations connected directly to our production machines through underground pipes. This greatly facilitates and speeds up our work.”
Eco-friendliness as a winning goal
From the beginning, the company has developed its cleaning systems implementing last-generation high-performance, low-environmental impact solvents, such as modified alcohols or hydrocarbons, in place of harmful chemicals. “When designing and building our machines, we pay particular attention to the self-cleaning devices with which all our systems are equipped, in order to reduce maintenance and therefore the operators’ contact with harmful cleaning agents,” says Sabbadin. “This green philosophy has always set us apart, starting from the look of our new plants: their external panels are decorated with an image representing our environmental policy, which was so appreciated by our customers that we are designing some more of them.”
IFP Europe’s successful systems
One of this company’s strengths is its ability to offer a wide range of different systems according to the type of cleaning process required. “Our washing machines can effectively clean any material and workpiece, from the smallest components, such as syringe needles, to large-sized parts up to one cubic metre. Our task is to create a standard system that can be subsequently modified depending on the workpieces and potentially integrated, for example, with an ultrasonic cleaning solution or with further baths. These modular systems are future-ready: if a customer wants to convert its production, we can intervene by simply adding some accessories.”
IFP Europe’s latest innovations include the HMA cleaning system from the KP series.
“Thanks to the possibility to operate completely under vacuum up to 1 millibar and to the wide range of standard and optional equipment, our KP series is the best cleaning technology currently available.
The HMA type ensures the best results in the most demanding applications in terms of productivity volumes and contamination levels. The structure of the machine has been completely revised to improve maintenance, accessibility, and above all quality standards and cleaning times.”
The series also includes the following types:
– KP Easy, with basic equipment but the best technology, suitable for installation in small and medium-sized companies;
– KP 30, perfect for very small parts, such as clockwork components;
– HD, particularly indicated for the removal of polishing pastes;
– MAX, IFP’s most sold plant, characterised by its large dimensions and enabling to perfectly treat very high production volumes or individual large-sized batches;
– Hybrid, presented at the Mecspe 2017 trade fair, the newest flagship technology of IFP.
Hybrid technology applied to cleaning
“With our Hybrid system, we have achieved previously unthinkable results for our sector,” states Sabbadin.
“The combined use of modified alcohol and an aqueous detergent solution ensures perfect cleaning with both organic (grease, oil) and inorganic contaminants (emulsions, salts).
This washing machine is more complex than systems using modified alcohols or hydrocarbons, in terms of both design and building. It has been conceived for companies needing to remove inorganic contaminants, such as salts, which are insoluble with alcohols; however, with organic residues like oil, an aqueous solution alone is not effective, because it emulsifies creating an uneven bath, since oil-contaminated water cannot perform a good cleaning action.
This is where our hybrid technology comes into play: we subject the workpieces to a modified alcohol cleaning stage to remove oil and then we eliminate the emulsified water; at the end of the cycle, we empty the chamber, dissolve the salts, and complete the process with the last alcohol cleaning stages. The component is thus perfectly clean.” This new solution has helped overcome the widespread belief that a modified alcohol plant is effective for removing oils, but not emulsions, since the latter require an aqueous solution.
“Currently, IFP’s customers include numerous companies that use an alcohol-based process to remove emulsions: the binding parameters are the type of emulsified water, the cleaning time and, in general, the production flow of the client, which can decide whether to perform a detergent-based cycle or not. In the latter case, the plant has the same function of a simple modular cleaning machine using alcohols. The possibility to add or exclude a cleaning stage with an aqueous solution is a further advantage for our customers, which can decide according to their treatment priorities.
To date, we have solved 85% of cases with our conventional solutions; in all other cases, we have relied on our hybrid technology, especially for turning companies treating brass or iron components with emulsions.”
A booming market
Despite its recent history, IFP Europe thanks to the skills of its team and to its willingness to bring innovative solutions to a market that is now ready to welcome new solutions, it has already reached several international customers, currently accounting for 40% of its turnover.
“The recent expansion of our headquarters will enable IFP Europe to become even more competitive globally. Our main target markets are the mechanical engineering, hydraulic, and medical industries. We aim at strengthening our relationship with companies in these sectors and, at the same time, making our technology known also in other fields. Our solutions can be successful in a vast number of applications and the green philosophy that distinguishes us is a further guarantee of reliability and safety of our plants,” states Sabbadin.
WHAT THEY SAY ABOUT US
Below are some articles written by our customers and published in the sector publications, describing their activities and how their use of our vacuum washing equipment contributes to the quality of their products.