MARCH 2014
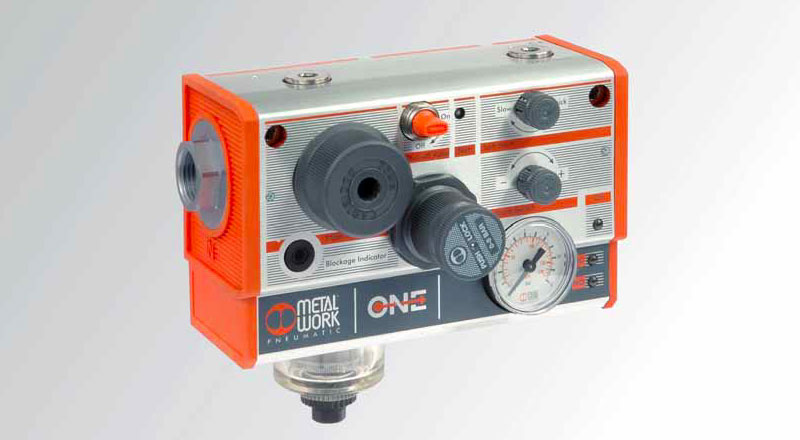
Download the PDF of the full article
METAL WORK
One solution for cleaning multi metal components treated with different cooling lubricants.
Problems arising from the cleaning of multi metal components
“Our previous cleaning plant,” Contessa continues, “was composed of hermetic units using perchlorethylene: This resulted in various problems, from the management and maintenance of the cleaning machines to the control of the environmental impact and the high consumption of solvent. Also the loading system of the eight containers was a complication, because it slowed down the production. First of all, however, it was necessary to solve the problem of the coolant lubricant solutions that dirty our components: During processing, we use two of them, a neat oil solution and an emulsifying fluid. The most critical aspect was finding a cleaning plant able to remove both fluids with the same excellent qualitative results.” Another factor to be reckoned with was the removal of chips from the milled products. They needed a machine able to remove the residue even only slightly anchored to the surface of the components: Besides the detergent action, a mechanical action on the surface of the workpieces was therefore needed. “Before choosing the current cleaning system by IFP Europe,” Contessa explains, “we have carried out several examinations and tested machines built by different suppliers. The problems, in most cases, concerned the cleansing of the parts.”
Read more
IFP Europe: One cleaning agent for all contaminations
One of the innovative features of the system developed by IFP Europe is the possibility to treat with the same machine workpieces from mechanical machining processes in which both cooling lubricant emulsions and neat oil are used. In accordance with the principle that “the like dissolves like”, aqueous cleaners are normally preferred for cleaning parts treated with emulsions, while the best results with neat oil are obtained with solvents. The ability of the designers of IFP Europe has been developing a treatment process that can deal with all types of contamination with the same cleaning agent, automatically managing also the various types of chip. “The modified alcohol plant by IFP, installed in January 2012, has enabled us to satisfactorily solve all the problems posed by our production process”, Contessa explains . “First of all, the cleanliness degree is optimal for all the components, regardless of the material of which they are made and of the cooling lubricant with which they are treated. Secondly, we can set the ideal cleaning cycle according to the type of material. The milling chips anchored to the components’ surfaces, finally, are now perfectly removed also thanks to the ultrasound technology with which the machine is equipped. The one-chamber system can handle four containers per cycle. We have thus reduced the downtime for loading the components: In one minute, the baskets with the products to be cleaned are ready for the treatment. As regards the duration of the cycle, we now clean the most complex parts in about 15 minutes, approximately half of the time needed with the previous plant. We can also perform faster cycles of approximately 8-10 minutes. In this way, we have been able to increase and almost double our productivity. We work in 3 shifts for 7 days a week and we can clean the parts for 21 hours per day. The system by IFP Europe also allows us to set the movement of the basket, depending on the characteristics of the workpieces that it contains: In the case of delicate components, we opt for a tilting motion, rather than rotating the basket of 360°, in order to avoid that the parts overturn and are somehow damaged.”
Reduction in consumption
The consumption of cleaning agents by Metal Work has been reduced considerably: In the past, the company purchased about 2 tons of perchlorethylene per year, while they now use few litres of modified alcohol per year. Contessa says: “That was our most important goal: Reducing the impact of our activities on the environment, in addition to the cost savings. This system has enabled us to do that. The new plant treats cooling lubricants and neat oils at the same time, continuously separating the emulsion, with an automatic water discharge device, as well as the oil from the solvent, with an automatic continuous discharge device. The machine also recovers processing materials such as chip, oil and emulsifier and enables their re-use by the machine tools. In particular, it treats the chip and separates it by type, sending it to one of the four appropriate filters with which the plant is equipped.”
WHAT THEY SAY ABOUT US
Below are some articles written by our customers and published in the sector publications, describing their activities and how their use of our vacuum washing equipment contributes to the quality of their products.